Introduction:
In this case, we will explore how our company successfully provided an automatic hollow block making plant to a customer in Uganda. The plant was designed to meet the customer's specific needs and overcome the challenges faced in the local construction industry.
Customer Background:
Our customer, Mr. Joseph Mukasa, is a prominent builder in Uganda with over 20 years of experience. He recognized the growing demand for quality building materials, particularly hollow blocks, which are widely used in the construction of residential and commercial buildings.
Challenges Faced:
The construction industry in Uganda faced several challenges, including a shortage of skilled labor, high production costs, and the need for consistent quality hollow blocks. Traditional manual methods were not efficient or cost-effective enough to meet the increasing demand for building materials.
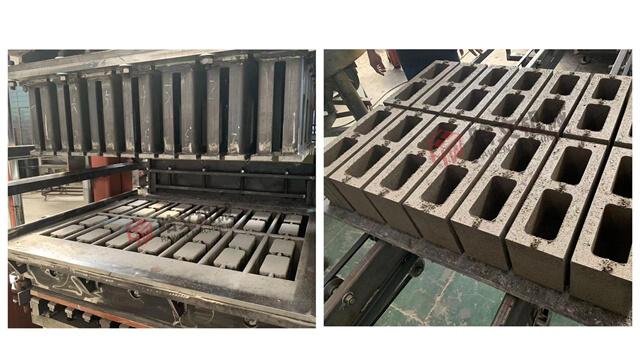
Solution:
Our team worked closely with Mr. Joseph Mukasa to understand his requirements and design a tailored solution. We proposed an automatic hollow block making plant that would address the challenges faced by the customer and provide consistent production of high-quality blocks.
Key Features of the Automatic Hollow Block Making Plant:
1. Automated Process: The plant was equipped with modern technology and machinery to automate the entire block making process. This reduced the dependency on manual labor and enhanced productivity.
2. High Production Capacity: The plant had a production capacity of 10,000 blocks per day, allowing Mr. Mukasa to meet the growing demand for hollow blocks in the region.
3. Quality Control: The automatic plant included quality control mechanisms to ensure that each block produced met the required standards. This eliminated the risk of substandard blocks being used in construction projects.
4. Cost Efficiency: By automating the process, the customer was able to reduce production costs significantly. The machine required minimal maintenance and consumed less power, making it a cost-effective solution for the long term.
Results and Benefits:
The installation of the automatic hollow block making plant brought several benefits to Mr. Joseph Mukasa and his construction business:
1. Increased Production: The plant enabled him to produce blocks at a faster rate, meeting the demand of his customers and increasing his revenue.
2. Consistent Quality: The automated process ensured that each block produced was of consistent quality, enhancing the customer's reputation in the market.
3. Cost Savings: By reducing labor dependency and optimizing production, the customer observed a significant reduction in production costs, resulting in higher profitability.
4. Time Efficiency: The automated plant saved time and effort, allowing Mr. Mukasa to focus on other aspects of his business and take on more projects.
Conclusion:
The successful implementation of the automatic hollow block making plant in Uganda demonstrates our commitment to providing innovative solutions tailored to meet the specific needs of our customers.
By addressing the challenges faced by the customer, we were able to enhance their productivity, improve the quality of their products, and contribute to the growth of the local construction industry.